
Source: GelSight
The Importance of Digital Surface Inspection in Additive Manufacturing
As 3D printing continues to take off and parts are used in more unique ways to solve complex problems, it’s likely that quality requirements will only become stricter.
3D printing, also known as additive manufacturing, is a revolutionary technology that enables the creation of parts by taking a 3D CAD file and adding the material layer by layer to create the final part. Unlike traditional manufacturing methods that involve subtracting material through processes like CNC or laser cutting, 3D printing builds objects by adding material only where material is needed. This process allows for intricate and complex designs that may be challenging or impossible to achieve through conventional means. With applications ranging from prototyping and product development to personalized healthcare and aerospace, 3D printing has emerged as a versatile tool, transforming the way we design, manufacture, and innovate in various industries.
With the limitless design possibilities of 3D printing you are able to design and produce custom parts that are not possible through conventional manufacturing methods. For example, 3D printing enables part consolidation by combining multiple parts into one single print, produces internal chambers for cooling and liquid flow, and accommodates designs featuring complex geometries for reducing weight or optimizing structures.
While the potential of what 3D printing can create is vast, this often means that the parts produced are needed for somewhat niche use cases. As a result, 3D printed parts are designed with precise specifications to meet the requirements of their applications, and the surface roughness of the final printed part can play a critical role in the overall part performance. While surface roughness is often associated with aesthetics, it can have major impact on:
- Functional Performance – In some instances, the surface roughness of the final printed part can increase functional performance especially in parts that need to slide, move, fit together precisely or will have contact with a moving fluid. A smoother surface reduces friction and allows for better functionality, while also ensuring the parts are more uniform than those manufactured by more traditional means and can pass rigorous inspection processes.
- Reduce or Eliminate Post-Processing – a 3D printed part with a smooth surface finish can reduce or eliminate the need for extensive post processing, saving both time and money. Parts with a rough surface may require additional steps such as sanding, filling, smuritropy, or coating to achieve the desired finish.
- Internal Chambers – One of the greatest advantages of 3D printing is the ability to design and produce parts with internal chambers for cooling and liquid flow. This is typically the case for heat exchangers which have seen their sizes reduced or their efficiency improved in a very significant way. These chambers are critical to the part’s performance but have limited access to allow for any type of post processing, making the surface finish a critical component to the overall functionality. The surface quality directly impacts the fluid dynamics within the internal channels. A smooth surface reduces the likelihood of turbulence, friction, and irregularities that can impede the flow of liquids or gases through the intricate pathways of the printed part.
The importance of smooth surfaces becomes even more pronounced when considering the risk of clogs or blockages within internal channels. Irregularities on the surface can create points of stagnation or turbulence, leading to the accumulation of debris or particles that may obstruct fluid flow. A smooth surface minimizes the likelihood of such obstructions, ensuring the reliable and continuous operation of 3D printed components.
Factors Influencing Surface Roughness in 3D Printing
Achieving a smooth surface in 3D printed parts involves a combination of precise design, layer thickness, and powder quality. Design considerations, such as optimizing support structures and minimizing overhangs, contribute to the overall smoothness of the finished part. Additionally, advancements in 3D printing technologies, such as high-resolution printing and post-processing methods, play a crucial role in producing components with the required surface quality.
The powder sphericity, granulometry, and quality have also been shown to have a direct correlation to the overall surface roughness of a printed part. Depending on the powders used, the surface finish of 3D printed parts can vary, and even the most minor differences in roughness can determine if a part meets the quality requirements to function properly.
Analysis of Powder Quality
The attached images, taken using GelSight Mobile, show two 3D printed parts, one made using powders from 6K Additive (Figure 1) and one using an alternative powder (Figure 2). High resolution digital tactile sensing devices can precisely visualize and measure the 3D topography of any surface, revealing microscopic structures that are difficult to detect using traditional inspection techniques. For additive manufacturing inspection processes, this precision surface analysis is crucial to identify those minor differences in quality and determine if a part is suitable for use.
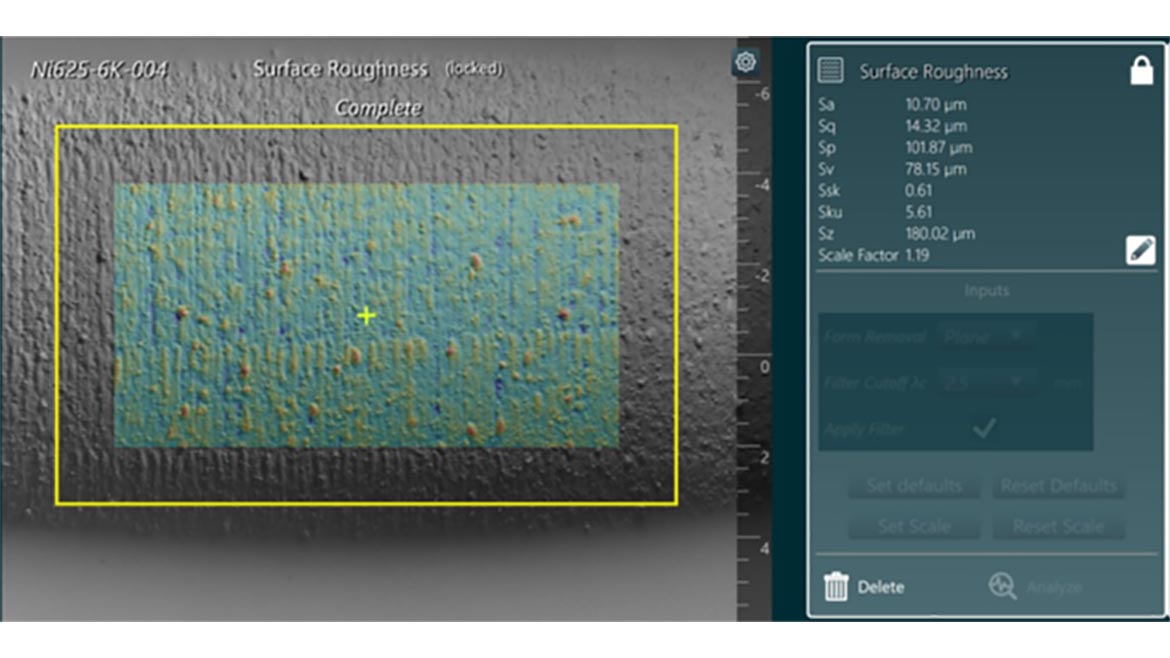
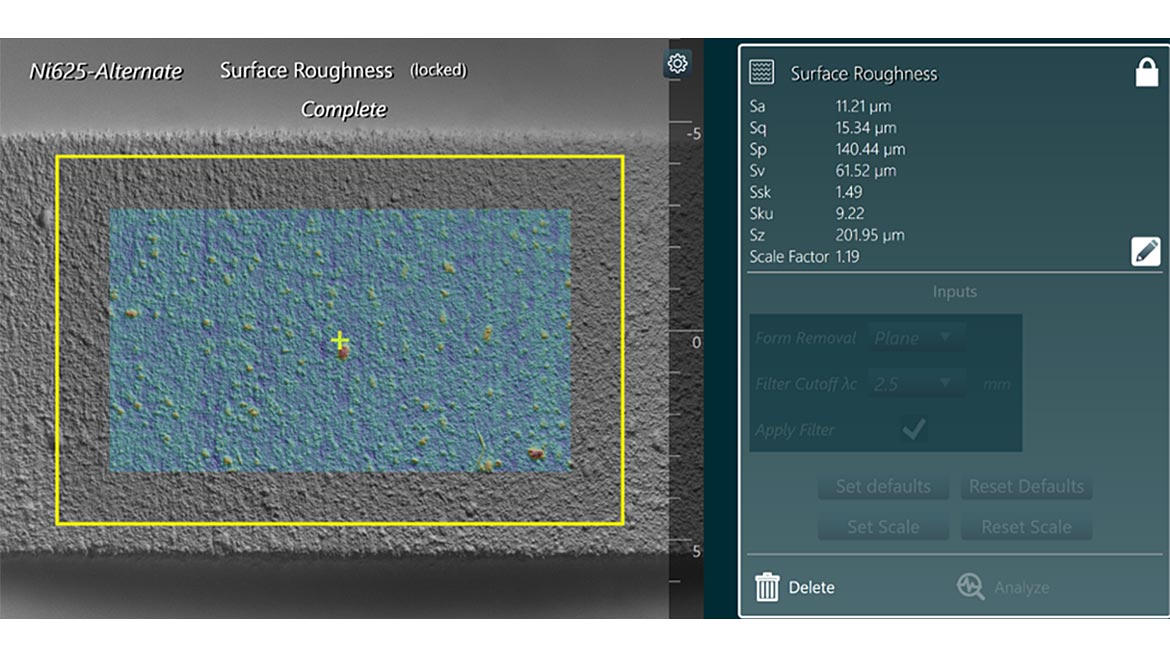
For example, based on the in-depth analysis on the two parts shown here, the surface roughness can be compared based on several parameters, including the average area roughness (Sa), root mean square roughness (Sq), peak height (Sp), pit depth (Sv), and more. These metrics each provide insight into different aspects of surface roughness, such as the size, height, depth, and standard deviation of the height distributions of surface imperfections such as bumps, pits, dents, scratches, holes and more. This analysis shows that the part in Figure 1 has a 6% lower Sa and 5% lower Sq than the part in Figure 2, meaning that the 6K Additive powder used to produce the part in Figure 1 resulted in a smoother surface finish.
While other aspects of the 3D printing process can influence surface roughness, this comparison demonstrates 1) the importance of choosing a powder with the right granulometry to produce a part with the necessary surface finish, and 2) the power of having a tool that can digitally inspect, measure, and analyze surface roughness at the micron-level.
Digitizing Additive Manufacturing Quality Inspection
Traditionally, the process of inspecting 3D printed parts has been done manually or required expensive and bulky stationary equipment, but digital tactile sensing technology significantly boosts productivity in quality control applications, regardless of the materials or surface finishes, including metals, polymers, ceramics, coatings, and more. Further, these advanced mobile metrology systems natively capture data on surface characteristics within milliseconds, with the click of a button, enabling repeated digital surface roughness analysis, and revolutionizing the way roughness measurements are currently done.
Surface roughness analysis is a crucial, yet complicated part of many R&D and production quality control inspection processes. In additive manufacturing specifically, the ability to simplify surface roughness analysis by allowing users to perform measurements in-situ, on any type of surface, with repeatability and speed makes it easier to ensure that you are using the best quality materials, and the parts will function as intended. As 3D printing continues to take off and parts are used in more unique ways to solve complex problems, it’s likely that quality requirements will only become stricter. As a result, new precise, digital surface analysis tools will be necessary to meet those expectations and help realize the full potential of many 3D printed parts.