Headquartered in Sainte-Claire, Quebec, PCM INNOVATION (PCM) designs and manufactures assembly lines, fixtures, and molds for high-precision parts. Its customers are world leaders in aviation, aerospace, and transportation. Many of the parts PCM manufactures have tolerance deviations in the thousandths of an inch. PCM has been successful, in part, by leveraging inspection solutions that enable a kind of agile manufacturing mode. What does this look like?
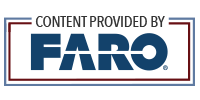
To fulfill its demanding contracts, PCM has established four facilities in three countries: Canada, the United States, and Mexico. The PCM team is also often on-site at client facilities. Operating in multiple locations presents multiple challenges, such as:
- Temperature variances
- Hardware brand differences
- Changing workload
- Contextual references
Temperature Variance
“On a 30 ft aluminum 7475-T7351 part, the elongation is going to be 0.020 in. for every 5 degrees Fahrenheit,” explains Sonny Harrisson, Senior Structural Inspector at PCM. “As you can imagine, mistakes can easily lead to scrapping a very expensive part that has a tolerance of ± 0.010 in.”
To mitigate issues with temperature differences, Harrisson’s team at the Montreal facility relies on FARO® BuildIT Software coupled with the FARO Vantage Laser Tracker.
BuildIT Metrology Software is a CAD-to-part inspection solution that enables quick and easy dimensional verification of manufactured parts and assemblies for tool building, assembly, alignment, process automation, reverse engineering, and quality control. BuildIT’s advanced analysis and reporting capabilities combine measurement data from multiple sources to produce detailed graphical and textual reports that are used to quickly identify manufacturing and production trends. With both numerical and graphical feedback of real-time deviations, BuildIT allows users to position parts with micrometer accuracy for high-precision assembly and alignment applications. BuildIT is NIST-certified and PTB-certified.
BuildIT Software compensates for temperature variances and adjusts data accordingly. Technicians from Canada can confer with their counterparts in Mexico and have comparable data.
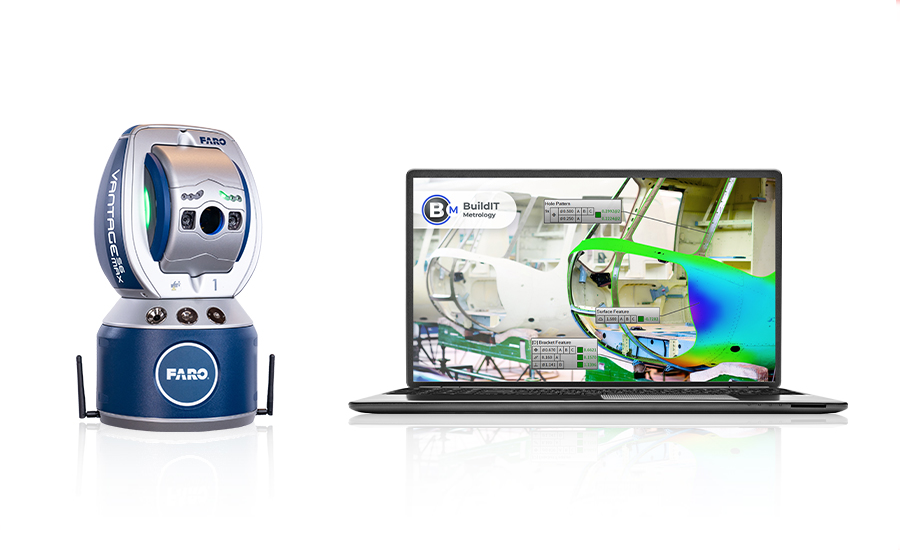
“Having the Vantage and BuildIT Software together is like having my own weather station,” quips Harrisson.“ The Vantage records temperature and humidity and sends the data straight to the BuildIT program. Then I can easily include that in my inspection report for our client.”
Hardware Brand Differences
Agile manufacturing may include the ability to operate on-site and interface with multiple brands of hardware.
“At our shop in Montreal, we only use FARO Vantage Laser Trackers. But, our other facilities and some of our clients also employ other brands of trackers,” explains Harrisson. “BuildIT Software is brand agnostic, so I can bring my laptop [with BuildIT installed] with me to any facility and plug into their CMM machine. When I can plug into their machine and verify that everything is all right, or solve a problem, it makes them very happy. There’s a lot of stress in the business, so we try to take some of that away.”
With 160 m (525 ft) of spherical working volume, the FARO VantageS and VantageE series laser trackers are world leaders in high-accuracy, large-volume measurement. The Vantage provides tremendous value in a complete laser-tracking solution that offers portability, accuracy, and great shop-floor durability.
Vantage Laser Trackers optimize workflow productivity for large-scale metrology applications including assembly alignment, part and assembly inspection, machine installation and alignment, and reverse engineering.
Changing Workload
Challenges also include normal variations in contract size and scope. PCM must be able to adapt to fluctuations in workload. Some work is handled by one technician; other contracts may involve working on a fuselage requiring four trackers in operation simultaneously.
“On a large project, we may have three laser trackers operating at the same time,” says Harrisson. “We may need to move each tracker three times in a day. We could easily end up with 50 to 60 total hardware movements.”
On occasion, the PCM inspection team needs more tracker operators than are available to finish a job in a timely manner. Reallocation of manpower requires a solution capable of accuracy and repeatability. PCM can rely on BuildIT’s automated inspection routines to speed up training technicians to fill the need.
“As a lead technician, I create inspection routines with BuildIT for junior techs to follow,” explains Harrisson. “I just record what I’m doing during an inspection, and the software creates the routine. When I’m done, I give the routine a descriptive name like, “hole inspection” or “surface inspection.” When another operator plays the routine, the laser tracker is going to point where he needs to inspect. Let’s say it’s a hole; it’s going to point to the hole. The operator records that measurement, and then the laser tracker is going to point to the next hole, and it goes like this. So, it goes twice as fast. We don’t have to tell BuildIT, ‘I’m inspecting this hole.’ It’s BuildIT that tells us, ‘You need to inspect this hole.’ It’s very simple.”
I don’t want to be software programmer, and I don’t want to have to call the software engineers just to use it. With BuildIT, I don’t have to.
- Sonny Harrisson, Senior Structural Inspector, PCM Innovation (PCM)
Contextual References
Although most 3D-inspection technicians will refer to coordinates as X, Y, and Z axes, there are some companies that still use industry-specific reference terms like “waterline.”
“When I do an inspection on an assembly for an aircraft, I may not use the coordinates X, Y, and Z in the report,” says Harrisson. “There are some clients who use ‘bus line station’ and ‘waterline,’ but I can go into the settings of BuildIT and edit the language to reflect what makes the most sense to our client.”
BuildIT also records a wealth of data that help PCM create additional value for its clients.
“I appreciate that I can go back to any point I’ve measured and retrieve all the associated information,” says Harrisson. “I can pull up what time and date it was recorded and who took the measurement. And I can edit the size and color of a point to differentiate and highlight it on a report.”
Having access to such data helps the PCM team establish a timeline for a specific operation and assess process efficiencies as well as job-pricing decisions.
One thing that doesn’t seem to vary are clients’ demand for extreme accuracy and a quick turnaround of orders.
To be successful in this industry, you must be very accurate, and you must be quick.
-Sonny Harrisson, Senior Structural Inspector, PCM Innovation (PCM)
Get in touch with a FARO representative to learn more here: www.faro.com