The Backstory
Carol Lake Metal Works faced a challenge: They were rebuilding heavy mining equipment — like worn-out sections on excavator buckets, loader buckets and haul truck boxes — but these machines frequently had complex, curved pieces that were very tricky to measure by hand.
A Newfoundland and Labrador-based company that supports the Labrador West and Northern Quebec Mining Industry, Carol Lake Metal Works reverse engineer and refurbish equipment from the IOC mine (Iron Ore Company of Canada), Tacora Mine in Wabush, Bloom Lake and occasionally ArcelorMittal.
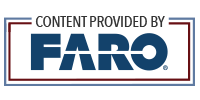
In the past, they’d taken measurements for parts with hand tools — tape measures, plus making cardboard templates with scissors and glue to model 3D shapes — which took hours of manual labor. And Jarret Wiseman, a Drafting Technician, was the man doing the measuring.
The Challenge: Tape Measures, Production Line Halts, Stress and Rework
The parts Jarret and the team in Labrador City reverse engineer daily — which entails cutting, breaking, bending and/or rolling — are complex and almost always huge in size.
“We do a lot of work with excavator buckets, boxes off the back of haul trucks and loader buckets,” Jarret said. “A fairly wide range of stuff in support of the mine. We’ll bring the equipment in, see the condition it’s in, like if some parts are worn thin — and we’ll replace those sections, adding wear parts and whatnot.”
Using a measuring tape worked, but it caused Jarret some trouble. It’s relatively simple to measure a flat surface with a tape measure. But the minute you work with organic parts that have compound curves, a tape measure becomes woefully inadequate. The effort (and inaccuracy) of measuring and drawing by hand introduced the opportunity for errors. If you want to know how painful it is, just ask Jarret.
“There was a little more stress involved when I’m trying to do big parts like that with a measuring tape,” he said. “The measuring process probably took me about an hour to an hour-and-a-half.”
Furthermore, the whole line would have to stop welding and gouging to allow him to take measurements. And with the sheer size of the parts they were refurbishing — like the entire side of an enormous haul truck box — Jarret couldn’t do the work just by himself; he had to ask other employees to help and hold the other end of the tape.
He quickly realized there was a better, faster and more accurate way to measure parts for reverse engineering and refurbishment.
Looking For a Solution
Jarret’s search for a solution led to the benefits of 3D laser scanning, and the FARO Freestyle 2 Handheld Scanner. Prompted by an email he wrote to the leadership team, everyone at Carol Lake Metal Works became interested in how it could optimize their process.
“Specifically, we were looking at speed and quality control. Wear parts with complicated, organic shapes are a typical thing that we do here. It can be fairly difficult to measure by hand. So, once I saw the handheld scanner, I thought would be perfect — because it would allow me to literally just scan, say, the side of a bucket, and then locate a wear plate right onto the side of it.”
The stereotypical tool of choice for reverse engineering is the FARO® ScanArm — but with the sheer massiveness of the mining equipment they were working on, Jarret and the team opted for the portable, versatile Freestyle 2, which perfectly suits their specific needs.
An Easy, User-friendly Tool to Learn
After acquiring the scanner in late 2020, Jarret found that it was easy to learn and use, right out of the box.
Which is good, because Jarret’s job often involves climbing and getting into weird places to get scans. Thanks to the portability of the Freestyle 2, Carol Lake Metal Work now avoids costly workflow disturbances and production halts.
“A lot of times the welders will already be up in the scissor lifts working on a machine we are refurbishing. And because the Freestyle 2 is so user-friendly, I’ll give it to the welder, and he’ll do a quick scan for me. I just set it up, tell him to push the button, point it at the area to be scanned; when the display shows it’s all scanned, hit the button and bring it back down.”
In addition, having the Freestyle 2 means that the company — and its employees — can stay safer and avoid climbing into dangerous positions to take measurements by hand.
“There have been a few cases now where I would have had to get up in the scissor lift, but because I have a handheld scanner that has such good range, I don’t need to get up in that scissor lift and put myself into those tricky positions,” Jarret said. “That was actually one of my arguments when I was proposing we pick up the Freestyle 2.”
The Impact: Fewer Production Line Disruptions, Greater Accuracy, Increased Safety
Six months down the line, what sort of impact has the Freestyle 2 made on the work Jarret does at Carol Lake Metal Works?
He says there are “far fewer disruptions” to production. Now, instead of having to get into a scissor lift, take his measuring tape out, and get in the way of workers to measure, he can actually get his fellow workers to do “a quick five-minute scan, and then we’re all back to work.”
Exemplary Projects: Quality Improvements and Fewer Reworks
Jarret offered two recent projects as examples of how the Freestyle 2 has benefitted the team at Carol Lake Metal Works. First, he showed some curved pieces that needed repair on a Hitachi excavator bucket. Second, he showed the walls on the Komatsu 930E that needed refurbishing — and specifically, a tricky corner piece on the haul truck box.
“What gets me excited is when I design a part and it’s got a really good fit. One of the most recent times that’s happened is the haul truck box, because there was a corner transition that met on five different planes. Now, before having the scanner, I don’t even know how I go about measuring that with a measuring tape. I guess my process would have been to cut a cardboard template, design the part, cut a one-eighth template out of one-eighth steel, check the fit, adjust, then do another template, just to make sure it fits — then, finally cut the part. But with the Freestyle 2, it’s just: Design. Cut.
When asked if he was surprised by how much time he’s saved since switching to the Freestyle 2 Handheld Scanner, Jarret’s answer was emphatic.
“Oh no, we knew right off the bat how it was going to be beneficial. I mean, just with the haul truck box project, it took me 20 minutes to scan both of those walls. If I had had to measure those up by hand, it probably would have taken me an hour, hour-and-a-half — just going around, measuring, reconfirming and whatnot. And it’d be fairly difficult too, because, you’ve got your taper at the back, then it comes up to another taper, into a chamfer. This isn’t a 90 either. This comes down on a taper and then you’ve got your bore or your lifting hole positions. So, yeah, it would have taken me a while without the scanner.”
Beyond the time savings and enhanced safety, the Freestyle 2 improves the quality of the overall output, the reverse-engineered part. In the past, even the most perfectly taken hand measurement would require a bit of re-work. The parts, when they’re cut, must be left slightly bigger than necessary, so they can be trimmed to fit. (It’s obviously much easier to trim a part down to size than it is splicing new metal onto the part to make it fit.) So, even though he was putting all of his time into measuring, Jarret knew getting an exact fit wouldn’t be possible.
This is not the case with the Freestyle 2 Handheld Scanner — now, Jarret is now able to skip the cardboard, scissors, glue and timely reworks. After using their Laser Scanner on the tricky corner piece, they locked in a perfectly cut part on the first try. Jarret said that getting a perfectly fitted part happens much more frequently now, too.
“It’s the best kind of feeling,” he said. “I’ll go down to the floor and the boys will come up to me and they’ll say, ‘Jarret, that part up in the corner, it fit perfectly.’ And I'm like: ‘Sweet.’”
Helping Carol Lake Metal Works Set the Standard
With the entrance to the mine just a kilometer down the road from the Carol Lake Metal Works shop, the work Jarret and the team does is vital to sustaining and improving Canadian mining operations.
“I’ve had a few requests now to specifically scan stuff because they knew we had it here. Word got around that we had one. And people are definitely interested in it, too. Typically, now whenever I go on-site to IOC, it’s me and the Freestyle 2 in that suitcase.”
Summary of Key Advantages:
Haul Truck Box Project
Without the Freestyle 2 Handheld Scanner |
With the Freestyle 2 Handheld Scanner |
|
Time spent measuring and its cost: |
6 hours @ $105/hr Cost: $630 |
1 hour @ $105/hr Cost: $105 |
Cost of halting production line: |
6 hours @ $105/hr 2 people Cost: $1,260 |
1 hours @ $105/hr 2 people Cost: $210 |
Cost of getting other employees to help measure: |
6 hours @ $105/hr 1 person Cost: $630 |
1 hours @ $105/hr 1 person Cost: $105 |
Cost of materials for potential rework: |
~$5,520 |
~$500 |
Total cost: |
~$8,040 |
~$920 |
Estimated total cost (for projects like this) over the course of a quarter: |
~$20,000 |
~$2,000 |
Estimated total cost (for projects like this) over the course of a year: |
~$80,000 |
~$8,000 |
*Note: Price estimates made in Canadian dollars, June 2021 |
Get in touch with a FARO representative to learn more here: www.faro.com