After years of robust growth and a burgeoning consumer economy with an ever-expanding appetite for privately owned automobiles, Covid-19 hit the world’s largest continent and its 4.7 billion people hard.
From China, as the first country to experience the impact of the pandemic, to ongoing microchip shortages in Taiwan (due in part to the island’s most severe drought in over 50 years and the high-intensity water needs of quarried metals) just as the world was getting back on its feet, many in the region are feeling exhausted.
But if the pandemic offers any collective silver lining, it’s in the lessons learned category. This is especially true in Asia’s automotive industry, a manufacturing sector that experienced a 10 percent production hit. Considering that Asia comprises more than half of the world’s vehicle production, this is significant. The key lesson learned is this: no matter what external global threat exists, be it Covid-19, terrorism, climate change, etc., quality control and inspection (QC&I) are at the heart of automotive industrial success. Not only in the QC&I as it relates to vehicles that come off the assembly lines, but the QC&I that goes into monitoring – and moving – the machines that form and stamp so many of an automobile’s 30,000 parts.

Image courtesy of FARO
Deviation Defense
The reality is, when a metal stamping machine/die stamps out thousands of blanks per day, it’s natural for deviations and alignment errors to occur. There’s also the need to react to new product designs when a new car model (or entire vehicle) is introduced, in effect re-introducing the possibility of new alignment errors. When deviation becomes great enough, a part no longer conforms to its established specs. If not caught early in-process, or during first-article inspection, cascading errors could arise. With supply chains already at risk, the automotive industry (and others) are looking for innovate ways to reduce these costly time and money mistakes.
Enter the world of sophisticated 3D Metrology software and hardware and its collective ability to provide the actionable insights that help automotive manufacturers overcome QC&I challenges. By providing faster, more accurate digital data to increase quality and throughput, metrology technology helps manufacturers make informed decisions to enable more predictive analysis, verify dimensional accuracy, and test tolerance. That’s true as it applies to customer satisfaction, or whether it concerns regulatory scrutiny, time to market, or a combination of all the above.
“A long time ago, you had traditional measurement methods, and these devices, measuring tape, calipers, micrometers, measure in 1D,” explained Jay Sakai, a Supervising Field Applications Engineer with the Japanese division of FARO® Technologies. “Then, newer technologies were able to measure in 2D. Now machines can measure in 3 dimensions and with products like laser scanners or scan arms, we can compare the part being measured with the project in programs like CATIA, Siemens, Pro/ENGINEER [now PTC Creo] and SolidWorks®.”
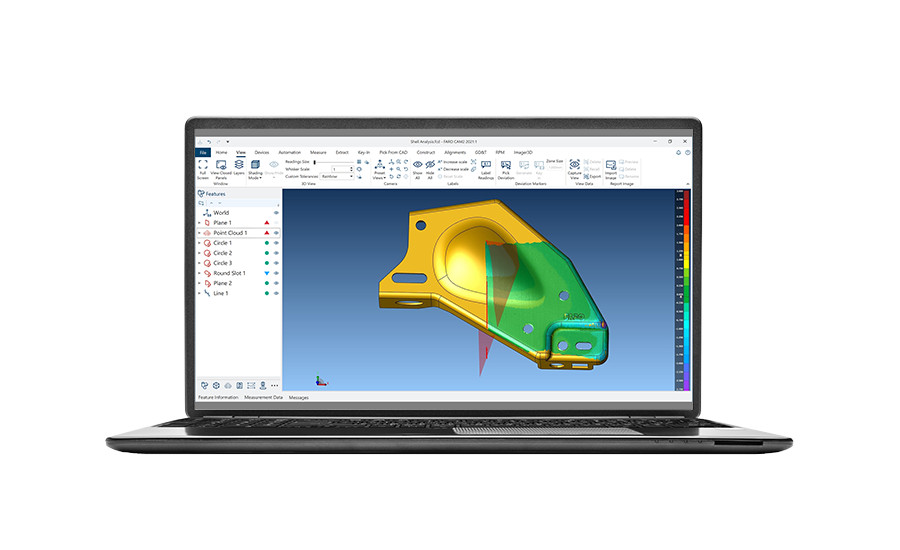
Image courtesy of FARO
From a metal stamping workflow perspective, these types of technologies have greatly streamlined what was once a cumbersome process. Stamping metal for automotive applications, is, naturally, a complex, multi-step operation, and is used in the creation of numerous automotive parts ranging from engine components to doors and other body panels. Often this assembly takes place in sub-assembly plants and the stamped parts are later shipped to a metal body shop where the entire vehicle is assembled.
When evaluating the metal stamping process, several factors must be considered:
- Stamping’s effects on the design functionality – are the stamped parts within the specified tolerances of the CAD model?
- Is the die consistently producing parts to the same specification? Are parts trending out of tolerance due to wear?
- All industry-specific requirements – Is the part safe and functional?
- What is the time required for production and quality control?
- Cost-effectiveness (what’s the ROI?)
Machine Interoperability
At each step in the process, 3D laser scanning and the ability to view, in real time, virtual representations of the captured data means that plant operators and systems oversight engineers have direct line of sight as to the accuracy, precision, and quality of the automotive stamping plants themselves, as well as the parts they manufacture.
“In Japanese companies and Asian companies in general that follow our lead, the most important thing is quality,” added Hideaki Itakura, a Senior Field Applications Engineer, also with FARO’s Japanese division. “So every part needs high quality. That’s why they increasingly rely on these types of machines. They are also looking to get work done faster and cheaper.”
But this is only the beginning of the technology’s reach. Beyond metal stamping itself, sophisticated 3D metrology measurement hardware and software is also able to determine the most efficient layout of the assembly line itself and how large, bulky machines (machines that include stamping) best align, where they belong on the factory floor, and even the spacing between machines. All of this can be achieved faster and with greater precision than ever before. What used to take days or weeks to complete, with a large commitment of staff, Mr. Sakai explained, can now be done in hours.
The next steps are twofold:
- The integration of multiple machines — scanners, arms, trackers, tracers, etc., — operating in a single software increasingly automated ecosystem
- The continued development of the automated factory where artificially intelligent robots can carry out parts inspection with little to no human intervention
While achieving the second goal is a little more distant, Mr. Sakai and Mr. Itakura are confident that the ongoing efforts of Asian automakers and partner companies will continue to push the envelope of what’s possible both from a hardware and software perspective.
“If you talked with Mr. [Henry] Ford a long time ago, if you saw his production line… and if he goes today to a Nissan factory, for example, or a Honda factory, where the robots are doing so many jobs he would say ‘My goodness, all automated,’” Mr. Sakai said. “But even today, parts of the production line are still not so automated. Quality inspection is one of them. We need the humans to check the machines and make sure they are aligned. This is something that we are working on and factory makers are working on. A lot of technologies will be necessary. One of them, AI, is here. It’s getting better. But it’s not perfect. Not yet. But I believe one day we will get there.”
As the world works to achieve stability and end the pandemic, Asia’s automotive comeback, thanks in part to advanced 3D measurement technologies capable of driving end-to-end efficiencies at reduced times and lowered costs, seems secure.
Get in touch with a FARO representative to learn more here: www.faro.com