
Electronics & Quality
Evaluating the physical properties of electronic devices and parts.
Whether you are working on an unmanned aerial vehicle or drone, a car, or an entirely new way to get around, such as a hoverboard, testing is a must. (Yes, hoverboards need testing too.) Physical evaluation testing is required in an increasing number of industries, including electronics. An electronic device that malfunctions isn’t just disappointing—it could also be dangerous. Therefore, electronic devices and parts require mechanical testing to ensure product reliability, compatibility, and performance. In addition, electronics must demonstrate that they operate according to existing electrical safety standards.
ASTM, for example, states: “ASTM’s electronics standards are instrumental in specifying, evaluating, and testing the performance requirements of the materials and accessories used in the fabrication of electronic components, devices, and equipments. These components include thin films and substrates, membrane switches, surface mount devices, electron tubes and emitters, integrated circuits, microelectronic devices, bonding wires, gas distribution system components, and flat panel displays. These electronics standards guide semiconductor device manufacturers and other companies that deal with such parts and components in the appropriate fabrication and treatment procedures, as well as in the examination and assessment of the end-products’ properties to ensure quality towards safe utilization.”
While the goal of quality and safety remain the same for many industries and applications, the type of test may vary.
According to the Encyclopaedia Britannica, “Materials testing breaks down into five major categories: mechanical testing; testing for thermal properties; testing for electrical properties; testing for resistance to corrosion, radiation, and biological deterioration; and nondestructive testing.”
The International Organization for Standardization (ISO) and the American Society for Testing and Materials (ASTM) have established standard test methods. Companies may test to industry and government standards for automotive and military/defense, including ISO 16750 and MIL STD 883.
Electronic components can be evaluated to detect defects such as joint cracks, voids, and disconnections. The term electronics encompasses a range of industries and products, including sensors, capacitors, consumer products such as cell phones and laptops, automotive components, and even ATMs. While a malfunctioning ATM may just be cause for frustration, electronics that prevent you from communicating on your cell phone can feel debilitating, and the errors from an automotive component can be dangerous.
Universal testing instruments offer a range of test options for electronics, including peel tests, shear tests, and cyclic bending tests. For example, the test jig could measuring the peel strength of the pins of IC chips; press vertically on the components to measure the shear strength; and observe fluctuations in resistance in response to cyclic loads in printed circuit boards. This allows for reproducing tests where thermal expansion and contraction of solder are repeated.
According to Shimadzu, “Heat generated internally in components during equipment operation and repeated ambient temperature fluctuations can apply stresses to the solder joints between the PCB lands and the surface-mounted component terminals, significantly affecting reliability. Therefore, it is important to evaluate the strength of the soldered joints, and one method of doing this is to test their peeling strength.”
Manufacturers have a range of choices whether they are looking for a testing solution for quality control or research and development (R&D). These solutions can be customizable to suit your particular application. Companies would do well to consider what method will be used and what specimens will be tested.
Even once you’ve narrowed down the options and selected a machine, you will likely still have more choices ahead in terms of different versions and accessories. Materials testing manufacturers offer a comprehensive selection of grips, compression plates, jigs, extensometers, and other accessories to choose from.
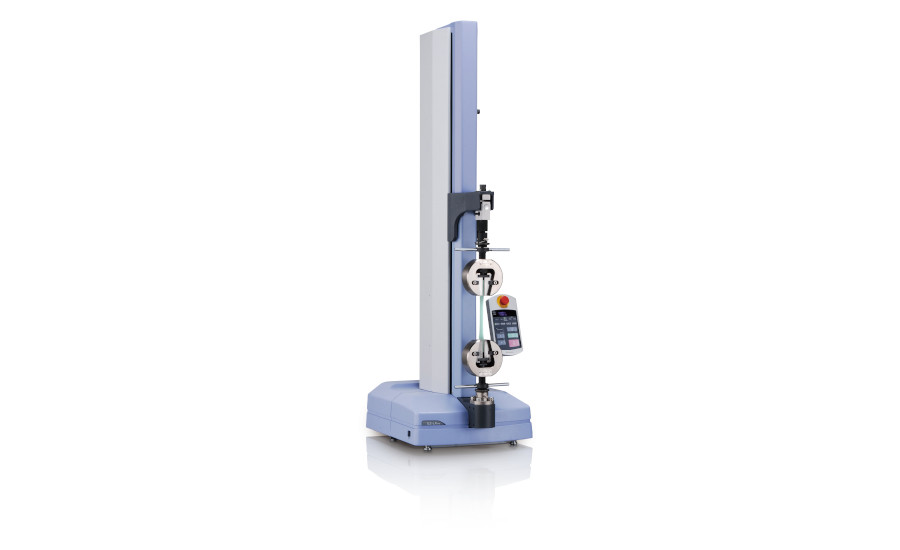
It’s also important to determine where the equipment will be used. What scenarios will the new machine encounter? What problems will it solve? Having the equipment on the shop floor can give manufacturers more control over their inspection program. The equipment may involve training to adopt the new solution but there are some bigger picture items to consider as well.
After the solution has been chosen, manufacturers should make sure that the electronics testing program is set up for success, in terms of procedures and best practices. While the testing process may initially seem intimidating, quality professionals should be aware of a few key steps to make the process run better.Before testing any electronic part or device, there are certain considerations to keep in mind. In “Testing Considerations for Electronics & Electronic
Components,” a Smithers Rapra webinar, the company provides some questions to ask before beginning the testing process:
- “What property should be measured?
- What is critical for the application?
- What key attributes must be replicated to achieve true, comparable results?
- What is the end of life or threshold criterion?
- How long should I test?”
In addition, the company suggests how to optimize a testing program and offers these tips:
- “Consider all possible external threats to your product
- Analyze the costs associated with testing
- Determine the costs associated with not testing
- Remanufacturing (rework) + labor + shipping
- Time lost (negative revenues)”
Ensuring compliance to a standard along with product quality is an important task for any manufacturer. The right equipment and testing methods can smooth the path towards a successful product launch. From there, innovations in mobile phones, laptops and even drones may not be far off.