More and more industrial manufacturers are moving towards automated solutions both to improve efficiency and solve staffing dilemmas. These jobs are often boring, repetitive, and/or prone to injury due to the work environment or the repetitive motion. The use of robots allows these positions to be filled permanently without the danger to human resources. While it is clear to see the application of robotics for jobs such as sorting, machine tending, packing, and palletizing, it may be less obvious how quality professionals can take advantage of automation. Though there are admittedly metrology applications which are less than ideal for robotics, there are many for which robots are well-suited that can save you both time and money. Imagine being able to free up your quality team from doing repetitive tasks and let them solve more complex problems to improve your quality processes.
There are two main categories of robots that we will discuss here: industrial robots and collaborative robots. Industrial robots are considered superhuman in that they move faster, are more precise, and can lift more than a human. Because of their speed and strength these robots require safety precautions including cage systems to protect the humans working in the area. Collaborative robots, or cobots, on the other hand are intended to be safe to work alongside humans. They move more slowly, have a lower payload, and have safety features such as force sensors to prevent injury.
Whether you are looking at industrial robots or cobots, automation can be a great solution for many reasons. First of all, they are far more consistent than a human could ever be. They are faster and they can work 24/7 without stopping for breaks. Though purchasing a robot may be initially more expensive, you can save costs over time. Often the jobs that robots perform are difficult to keep staffed with human labor. The jobs are repetitive and boring, making them less than desirable positions. Finding a reliable labor force to staff these roles can be incredibly difficult. Continually having to rehire and train human labor is expensive, even when qualified applicants are readily available.
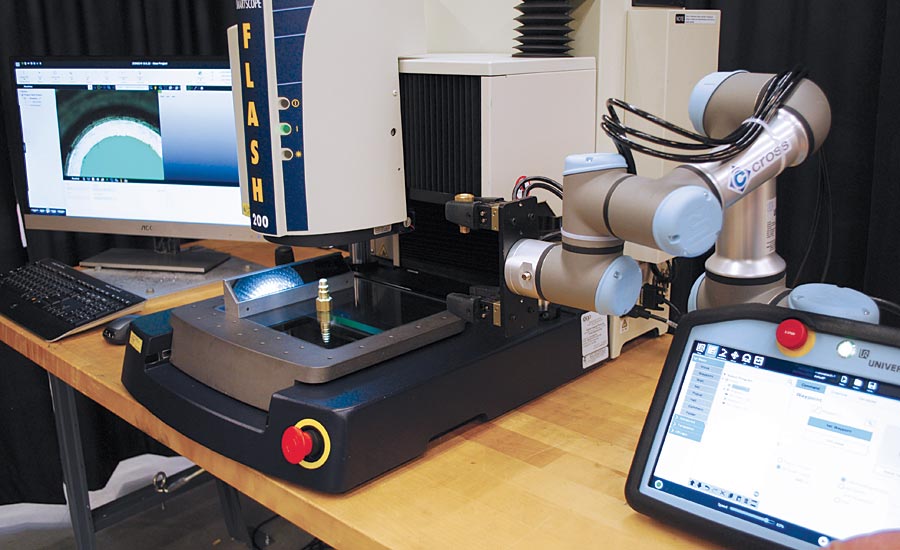
Cobots can be programmed to communicate directly with video measurement equipment, allowing them to place parts and then sort parts based on the data collected.
Additionally, manufacturing environments can be dirty and/or dangerous and the motion is typically highly repetitive, making injury common. Though the safety of the environment may be less of an issue in a quality lab, the process of inspection is certainly repetitive. Whether the injury results from a workplace accident or is a repeat use injury such as carpal tunnel, the cost for even one injury can far exceed the cost of a cobot. Robots can also be advantageous for your current workforce, because by automating menial and repetitive tasks, you can move your human resources to more interesting and engaging work elsewhere in your facility.
There are two main quality tasks for which robots are ideal: machine tending and visual inspection. Robots are perfect for machine tending because it is a highly repetitive task that doesn’t require human interaction. They simply load parts into inspection equipment for measurement and sort them based on the results. Whether you need pieces loaded one at a time into a video measurement machine, or you need to load multiple pieces into a fixture on a CMM, robots can easily load, unload, and sort based on the outcome. Force sensors on the end of arm tooling, or EOAT, can allow them to carefully and precisely load parts into more complex fixtures. Your robot can be programmed to communicate directly with the measurement equipment, telling it which parts are good or bad and then placing those items into the appropriate bins or boxes to move to the next step in the process. Additionally, they can keep record of each part that they have touched and sorted, providing the user with valuable information about which parts passed and which did not, as well as where they were placed after measurement.
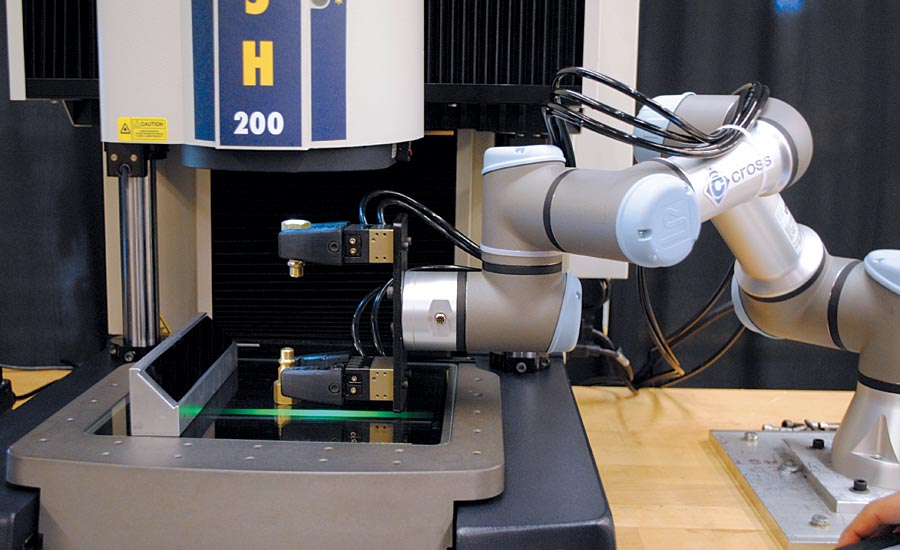
End of arm tooling can be customized to parts and hold multiple parts in order to decrease cycle time.
The second application that robots are great for is visual inspection. If you have pieces coming through that need to be inspected for various features, a single robot with a camera mounted on the end can replace multiple cameras. This is most advantageous for instances with a high mix and low volume of parts, meaning that there are often line changeovers but the throughput is relatively slow. If you have multiple cameras mounted that all take a picture at once, the throughput is faster but the changeover is significantly slower.
As with any other technology, there are some drawbacks and considerations for quality professionals when it comes to incorporating robotics into your quality processes. In precision measurement applications with tight tolerances, robots may not be suitable for directly taking measurements with a probe or a scanner. To put this into perspective, stationary CMMs typically have a tolerance of +/- 3-7 microns, and portable CMMs have a tolerance around +/- 25-50 microns depending on size. Robots meanwhile can have a tolerance of +/- 20-500 microns based on the size of the robot, with smaller arms being more precise. Although technology is constantly improving, at this time, the encoders in robot arms are not capable of the high precision of a CMM, which could be considered a very precise robot. Another consideration is that robots do not compensate for thermodynamics, which in some circumstances can result in issues with repeatability and reproducibility. For this reason, when making very precise measurements, the robot arm will introduce a number of uncertainties to your measurement protocol that could make it less than ideal for high precision measurement.
All of that being said, tolerances and uncertainties associated with robots are not necessarily an issue for all applications. If your measurement application requires looser tolerances a robot with a probe or scanning head may be a measurement solution. For instance, you can attach a scanning head to a robot to take measurements of stamped metal parts using fringe pattern analysis which is a great way to automate a measurement process.

Cobot visually inspects a part to ensure certain features are present.
When it comes to deciding if automation is right for your quality process, it is critical that you talk with a measurement professional as well as a robotics expert. A metrologist can help you to determine the needed tolerances and whether or not automation will impact your measurement data. A robotics expert can also walk through the capability of the robot, necessary programming, as well as help you with a risk analysis to make sure that robots are safe for your work environment.
The great news is that technology is moving quickly and it is likely in the near future that robots will be able to handle even more advanced metrological processes. This is exciting because most inspection labs and quality teams are currently spread thin. Not only will automation free up human resources to do more complex jobs, it will also help to improve consistency in quality processes and improve throughput. V&S