On March 24, 2004, Sikorsky Aircraft Corp. recognized its metrology lab team with its first-ever Achieving Competitive Excellence (ACE) Gold Cell. ACE Gold represents the highest level of quality at Sikorsky and its parent company, United Technologies.
Former Sikorsky President Steve Finger presented the team with the award, citing the team's milestone achievement, and its demonstration of world-class levels of quality, efficient delivery times and cost reduction.
What is ACE Gold?
ACE Gold represents world-class business performance and metrics, highly engaged, motivated employees who drive a culture of "routine excellence," and ultimately, satisfied customers.The ACE program includes a suite of tools to facilitate continuous improvement, and in conjunction with implementing Lean manufacturing, is how Sikorsky runs its business.
The metrology lab is responsible for calibrating some 37,000 gages and measurement tools used by Sikorsky each year. The lab team's process for achieving ACE Gold status required a self-assessment of each work area. This effort includes the examination of metrics, motivation, processes and people. Each category includes specific criteria rated 1 to 10, such as the presence of effective metrics, accountability, use of the ACE tools, customer/
supplier alignment, training, communication and leadership.
The self-assessment was followed by a rigorous independent evaluation that focused on appropriate ACE tool usage, premier results and ensuring the culture could sustain the quality improvements. The lab is a regular stop on company tours and United Technologies' Ito University-a Learning Center formed to educate business units on the ACE operating system.
Even a brief visit to the lab shows how the team has further improved its performance. The work area is clean, well organized and brightly lit. Energetic, creative employees staff it. They are eager to share what they are working on and always open to feedback on how they can further improve their performance.
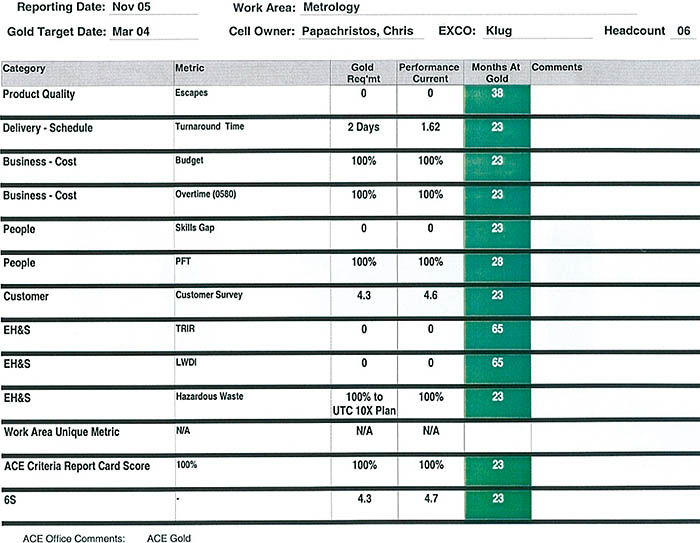
The team also is implementing communication improvements by updating its equipment management system (EMS) database and periodically reviewing point-of-contact lists to ensure they are current. The team is working with Sikorsky's human resources to link the HR database with EMS to automate the lab's notification system, which is used to communicate with customers when an item is due for calibration. The team is busy planning further improvements, including:
-Implementing a new automated calibration labeling system that will reduce the calibration process of items in the lab.
-Identifying measuring and test equipment candidates for in-house calibrations vs. supplier calibration to achieve improved cycle times and reduce costs.
-Reviewing the top five dimensional gage categories' calibration intervals and metrology engineering procedures for possible interval extension that consequently will result in additional calibration system efficiencies.
Metrology's Use of ACE Tools
Using the ACE tools, including value stream mapping, the team has made dozens of process improvements. For example, it has reduced its backlog of 830 items by 81% in January 1999 to 155-the current year-to-date process average. Lead-time has been reduced by 93%, from 18 days in queue on average to 1.5 days. The other process improvements include:-Introduction of a setting master to check depth micrometers.
-Introduction of bar coding to help track tools and quicken processing time.
-Transition to a torque wrench calibration machine that calibrates the tool in five places and at five different torque levels.
-Implementation of a laser bench micrometer, which checks concentricity by measuring drill pins in three places; measurements are made in 0.1 second.
The team for the first time in January 2004 reduced its overdue gages to zero- ahead of its own plan, for the first time in a long time. This result was driven by use of value stream mapping and commitments made by suppliers and customers, and Sikorsky Operation Centers.
Safety First
On January 17, 2006, the product integrity metrology lab team celebrated an important Environment, Health and Safety (EH&S) milestone, reaching 2,018 days without a team member on-the-job injury.The team's 6S-safety, sort, straighten, shine, standardize, sustain-improvements are focused on the appearance and functionality of the lab. The team philosophy is "first impressions say it all."
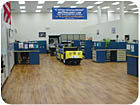
Visitors notice the floor first. Customers-both internal and external-are impressed with the lab's clean and organized appearance. The metrology lab strives to operate as a world-class example of how neatness and clutter-free work areas invite a safer and more efficient environment. The team prides itself in knowing that, when a customer leaves the lab, they feel confident that they will have a quick turnaround of their measuring and test equipment needs.
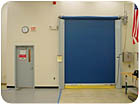
There have been recent 6S improvements. A new roll-up door allows easier access to the lab by tow motor drivers who come by regularly to retrieve tools and gages for delivery to offsite locations. Drivers can now open the door themselves and not interrupt ongoing work.

New storage cabinets allow employees to work safer. The old six-foot-tall cabinets impaired employees' visual scope. The new cabinets are four-feet tall and employees can see over them easily. The cabinets are also better organized and do not require an extended reach to obtain parts and tools. The lab continues to identify and implement 6S improvements.
Metrology Lab's Future
As the metrology lab makes further progress toward recertification to ACE Gold, the team knows the value of making 6S an ongoing priority and continues to see the value of each improvement in the direct and tangible benefits observed every day.Carl Lucas, manager of product integrity core services, believes building and sustaining a highly motivated work team is the key to success. He says metrology lab team members are successful because they believe in the benefits of ACE and in the application of the ACE Tools in everyday work.
Feedback is continuously collected, giving employees a sense of pride to know that they have a great team in the metrology lab-people who are willing to do whatever it takes to keep their customers satisfied.
QUALITY Tech Tips
-The metrology lab team's standard process includes each work area completing a self-assessment that covers metrics, motivation, processes and people.-A laser bench micrometer, which checks concentricity by measuring drill pins in three places, makes measurements in 0.1 second.
-Sikorsky has transitioned to a torque wrench calibration machine that calibrates the tool in five places and at five different torque levels.